Application
Lateral Flow
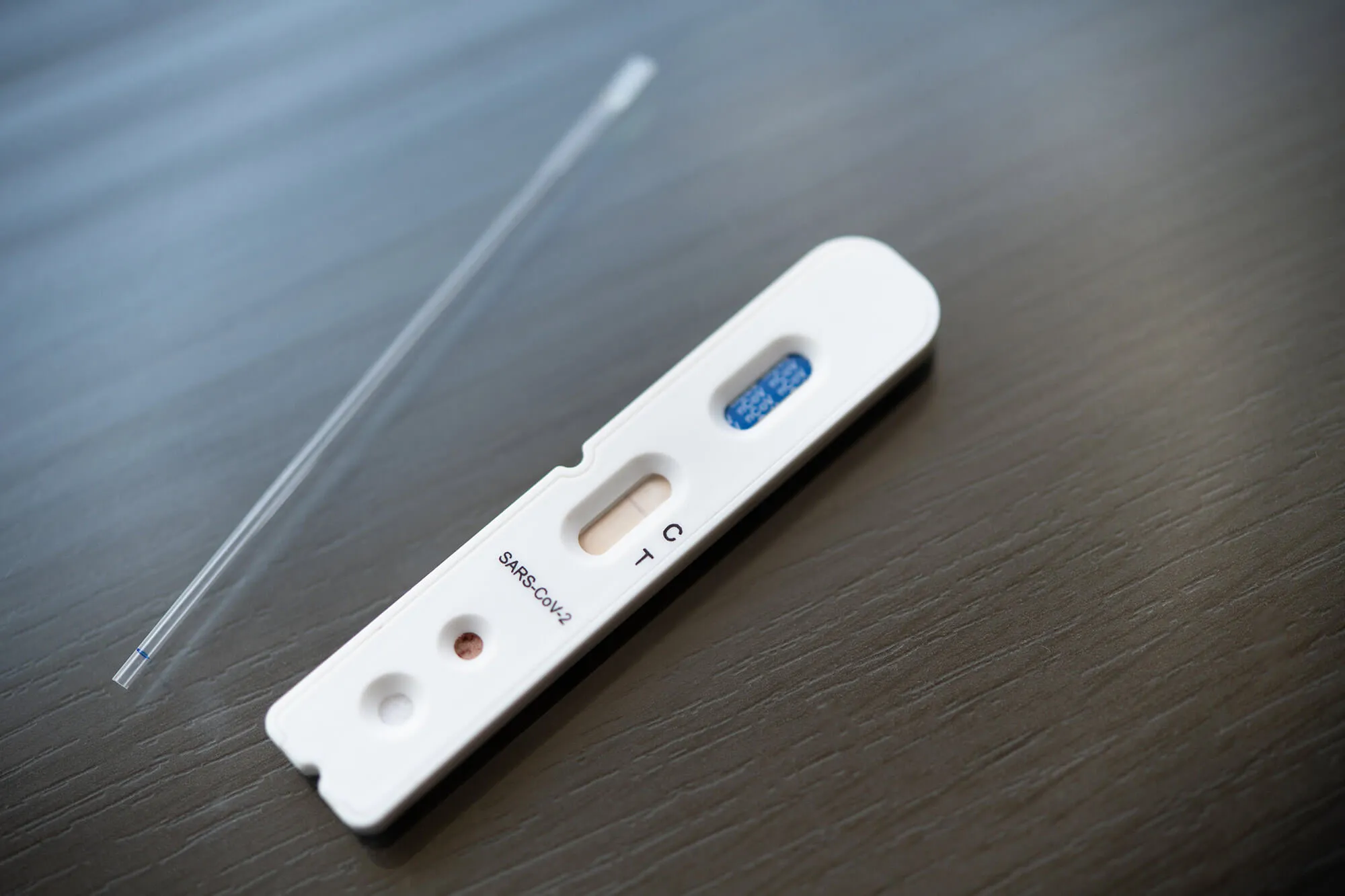
BioDot is the premier equipment provider to the lateral flow device industry. Since 1994, its dispensing, cutting and lamination technologies have enabled developers and manufacturers to create high quality lateral flow tests.
Lateral flow applications using BioDot technologies:
- COVID-19
- Infectious diseases
- Allergies
- Biomarkers
- Food mycotoxin & allergens
- Drugs of abuse
- Pregnancy and fertility
- Veterinary
- Agriculture
- Sexually transmitted diseases
Highlight
COVID-19
More than 80 companies worldwide, including the world’s largest diagnostics manufacturers, use BioDot’s systems to produce POC antibody, antigen and PCR tests for COVID-19.
BioDot’s low-volume roll-fed dispensing platforms and automated lamination systems are critical for high throughput. Each work cell, or instrument platform, has the ability to produce up to 100 million tests per year, allowing customers with multiple systems to rapidly scale and sustain production volume.
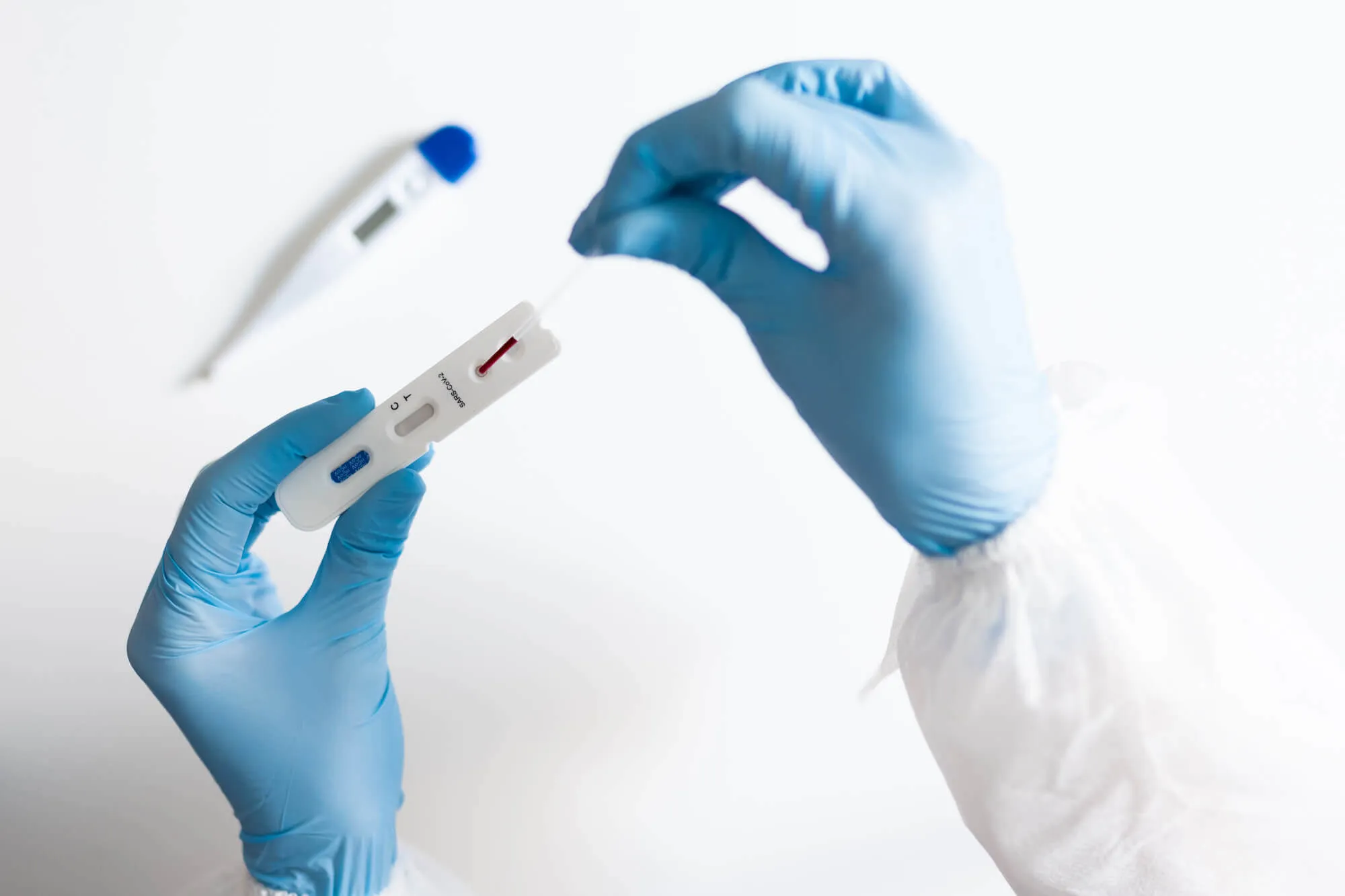
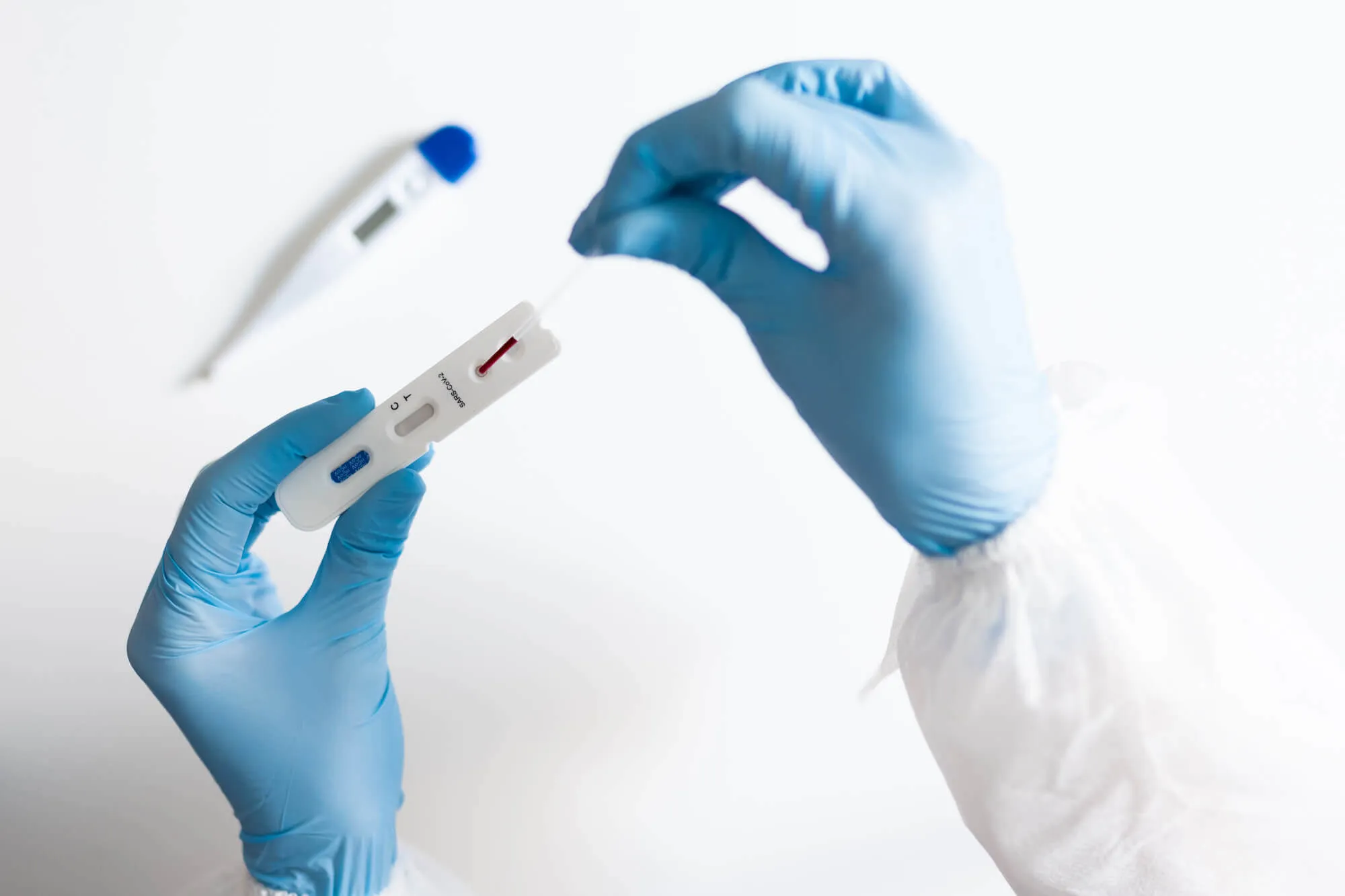
Lateral Flow Products
Highlight
Highlight
Highlight
Highlight